VisionGauge�
Latest Improvements
VISIONx INC.
is always working to improve VisionGauge�. The main improvements and
new
features that have been added to VisionGauge� (version 5.45) since the
previous major release (i.e. version 5.00) are the following:
-
VisionGauge� is now compatible
with TWAIN-compliant image acquisition devices (e.g. digital cameras,
scanners,
frame grabbers, image databases, etc...).
-
We.ve added support for
the Integral Technologies Inc FlashBus MV™ family of video acquisition
& display boards (see www.integraltech.com for more information
about
these boards).
-
In the Manual and Motorized
Stage Configurations of VisionGauge�, it is now possible to set the
stage
position to zero along any single axis (rather than along all of the
axes).
-
We've added an "Image
Sequence capture" tool you can use to capture & display images
at a
given time interval (every 5 seconds, for example). The images can
either
be displayed in "normal" or "full screen" mode and the images can also
be saved to disk, either in BMP or JPEG formats. This new tool is very
useful when observing & characterizing time-dependent processes.
-
A new "Arbitrary Line
Width" measurement tool has been added to VisionGauge�. It works very
much
like the existing "Line Width" measurement tool, in that the user draws
a box that over-reaches a line (e.g. a trace on a PCB, etc...) on the
image
& VisionGauge� then automatically finds the line &
precisely measures
its width. However, whereas the existing Line Width tool was limited to
horizontal & vertical lines, this new measurement tool has no
such
restriction & can deal with lines of any orientation.
-
We've added a new image
analysis tool to VisionGauge�: the new "Edge Map" tool in the "Tools"
sub-menu.
It basically passes the image through an edge-detection filter
& displays
the result.
-
Also, the "Overlay Image"
window now has a few new "Image Artithmetic" function. Previously,
VisionGauge
only allowed for image superimposition (with a variable transparency)
and
image differencing. Now, we've also added image subtraction &
addition
as well as "min" and "max" operations. These new image arithmetic
capabilities
can be very useful, for example when you're working with thresholded
images
for "Counting & Sizing" operations.
-
We've added two new Annotation
Modes: "Count" & "Box". As its name implies, the "Count"
feature is
used to manually count particles, blobs and other such objects. The
user
can specify the base (or "starting") number used for counting. This is
useful if - for some reason - the user interrupts the count &
wishes
to resume or continue counting later on. The count feature also has a
"Sizing
Annulus" which can be activated or not. It is also possible to specify
the diameter of the annulus (in the current measurement unit
system).
-
As for the "Box" feature,
it simply lets the user draw a rectangular box on the image. Here also,
the user can set the size (i.e. both width & height,
independently)
of the box, once again in the current linear measurement unit system.
And
as is the case for all of the annotation modes, for both of these new
features,
line colors, styles, thickness as well as font sizes, types, colors,
etc...
can be set using either the Annotation toolbox's "Preferences" button
or
through the "Settings | Annotation Preferences" menu command.
-
In the manual- and motorized-stage
configurations of VisionGauge�, it is now possible to apply Linear
Error
Correction (i.e. LEC) along the Z-axis, as well as along the X- and
Y-axis.
-
We've developed VisionGauge�
HT to measure the hardness of materials. VisionGauge� HT automatically
determines the hardness (Brinell, Knoop, Rockwell & Vickers) by
visually
measuring characteristic dimensions on indentations made by standard
hardness
testing machines. VisionGauge� HT carries out all hardness measurements
in accordance with the latest revision of the relevant ASTM Standards.
And VisionGauge's� advanced edge-detection technology produces
sub-pixel
accurate measurements, increase measurement repeatability and virtually
eliminates operator-dependent measurement error.
VisionGauge�
HT is a superset of VisionGauge's� feature-rich Standard Edition, which
means that it includes VisionGauge's� wide range of measurement and
statistics
tools, counting & sizing features, reporting &
databasing capabilities,
image capture, annotation, enhancement, analysis, comparison &
transmission
features, etc...
-
When carrying out diameter
& radius measurements, it.s now possible to use up to 6
measurement
points. When you use more than 3 points, VisionGauge� finds the "best
fit"
circle.
-
When no file extension
is given (for any type of file: image, data, "rtf" report, etc...), an
appropriate default extension is now automatically added to the
filename.
-
It is now possible to
send the current stage position to a data file by pressing the "Output"
button in either the DRO or "Motion Toolbox" windows. It should be
noted
that a data file must have previously been open (using the "File | Data
| Open" menu command).
-
Live Image Overlay Builder
has been enhanced: it's now possible to use circles & arbitrary
line
segments. We've also added an option to the "Live Image Overlay" window
that allows you to add the live image overlay over top of the image
when
you "freeze" it.
-
We've added simple password
protection for calibrations & stage-based Linear Error
Correction (LEC).
-
We've also added a second
level of password protection, that we call "Lock-Out" password
protection.
When "Lock-Out" password protection is enabled, VisionGauge� prompts
the
user for the "Lock-Out" password whenever the user attempts to:
i) write setup files
to disk
ii) change the system's
"general preferences" (i.e. through the "Settings | General
Preferences"
menu command)
iii) write motion
programs to disk (in the Motorized Stage Configuration)
iv) change the motion
control settings (i.e. through the Motion Toolbox's "Settings | Motion
Control" menu option in the Motorized Stage Configuration)
v) send commands directly
to the motion controller (i.e. through the Motion Toolbox's "Command"
menu
option in the Motorized Stage Configuration)
-
We've broadened &
enhanced VisionGauge�'s support for JPEG image files.
-
We've added a marker to
VisionGauge�'s Calibration Toolbox to indicate which calibration is
currently
loaded into the system.
-
We've enhanced VisionGauge's
support of EPIX's PIXCI� D video acquisition board for digital cameras.
Among other improvements, we've added some support for live image
overlays,
as well as for reading-in a PIXCI� D format file (*.fmt) containing
the description of a video state and created with XCIP/XCAP.
-
We've added a new measurement
mode (for 3D stage-based systems) that allows you to measure the
distance
between a point and a plane. This new measurement mode is very useful
for
very high accuracy thickness & height measurements (i.e. "Z
measurements"),
when you want to compensate for any co-planarity error between the XY
stage
and the sample. This new measurement mode is very simple to use: simply
select four (x, y, z) points in space. VisionGauge� then fits a plane
through
the first three points and measures the shortest distance between this
plane and the fourth point. As always, VisionGauge� updates the
measured
value as you're carrying out the measurement, making it very easy to
"see
where you are".
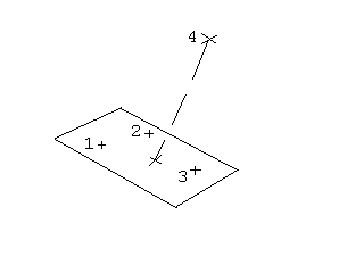
-
We've added support for
the SPOT(r) RT digital camera.
-
The reporting for Vickers
Hardness Testing has been vastly improved, and now allows for the
collection
of samples with statistics, added "depth" fields, output of graphs,
etc...
We've also improved the integration of the hardness measurements with
the
other features.
-
New controls have been
added to the "automatic arbitrary line width" measurement tool.
-
We've enhanced VisionGauge�'s
"Counting & Sizing" feature so that it can be used to obtain
information
about individual objects (such as grains, particles, cells, etc...). To
obtain
the area and equivalent diameter of a specific object, simply click on
it from within VisionGauge�'s "Counting & Sizing" window.
Furthermore,
the "Counting & Sizing" window's "File | Save as..."
menu command
now lets you save to disk the information about all of the individual
objects
in the sample, along with the rest of the sample information.
You can also remove
one or many objects from the sample by pressing on the "Counting
&
Sizing" window's "Remove" button and then clicking on the objects that
you want to remove from the sample. The image of the objects as well as
the "Counting & Sizing" window's results are automatically
updated.
Please note that when you click on an object to remove it from the
sample,
VisionGauge� stores the coordinates of the pixel on which you clicked.
This way, even if you subsequently change the parameters in the
"Counting
& Sizing" window, any object that passes through these
coordinates
is automatically removed from the sample. To "un-remove" all of the
previously
removed objects, simply press on the "Counting & Sizing"
window's "Un-remove"
button.
- We've added support in
VisionGauge� for EPIX's PIXCI� SV4 video acquisition board for
Composite
& S-Video analog cameras.
-
We've improved VisionGauge's�
motorized stage control by implementing a form of torque feedback when
instructing the motor controller to "switch modes". This results in
significantly
smoother acceleration & much quieter motion, even under heavy
loads.
-
We've enhanced the "teach
mode" in VisionGauge's� "Motion Toolbox" so that it is now simple to
add
instructions within a motion program to change the measurement mode "on
the fly", automatically. Furthermore, all of the "measurement mode"
information
associated with a motion program is saved to disk within the motion
program
file and can thus be recalled for later use.
-
We've added a marker to
VisionGauge�'s Calibration Toolbox to indicate which calibration is
currently
loaded into the system.
-
More state variables are
now saved to "Setup" files, including the system's current "measurement
mode".
-
We have added a "Focus-Based
Image Blending" tool (i.e. "Perfect Focus"). You can use this new tool
can combine two or more partially-focused images into one fully-focused
image! This is extremely useful in applications where your instrument's
optical depth-of-field is less than the height of the features
& topography
on the sample. This is a fully-automatic tool that works on color as
well
as greyscale images, and there is no limit on the number of component
images
that you can use.
With this tool, you
can choose from 4 different automatic image-blending
algorithms:
1. Best focus
2. Weighted focus
3. Power-weighted focus, and
4. Adaptive (i.e. neighborhood-weighted best focus).
In practice, the 4th
algorithm generally gives excellent results (and is always active by
default),
but the other 3 schemes are also available to give advanced users a
maximum
level of flexibility.
- The Motion Toolbox's "Stop"
button now acts like an "emergency stop": now, all motion stops
instantly,
regardless of how the motion was initiated.
-
In the Motorized-Stage
Configuration of VisionGauge�, we've added joystick support for a 3rd
axis
(i.e. Z-axis).
-
New controls have been
added to the "automatic arbitrary line width" measurement tool.
-
In the Motorized-Stage
Configuration of VisionGauge�, a number of "advanced" motor control
settings
have been added (for initial velocities, hold & run current,
number
of ramp-up & ramp-down steps, etc... )
-
In the Motorized-Stage
Configuration of VisionGauge�, we've added "convergence criteria" (you
can specify distinct values for the x, y and z axes). By default, these
values are zero (i.e. when carrying out a move, VisionGauge� should
attempt
to reach the exact position). However, by setting looser criteria (i.e.
larger values), you allow the stage to stop on a position that is
slightly
off from the prescribed position. There are many instances where such
very
slight off-positions are acceptable and "loosening" slightly the
convergence
criteria can speedup motion considerably (because fewer fine
convergence
iterations are necessary).
-
In the Motorized-Stage
Configuration of VisionGauge�, we've added support for three joystick
buttons
(i.e. to switch between the 3 jog velocities).
-
We've added new "Database
Search" tools and a "Thumbnail Preview Image Gallery" to VisionGauge�.
You can use these new tools to call up all of the reports in
VisionGauge's�
report database that contain a specific search string (for example: a
date,
an evocative keyword, a specialized term, etc...). Searches can either
be
case sensitive or not. These enhanced "Database Search" tools work
seamlessly
with VisionGauge's� integrated Report Generator and Database.
To carry out a search,
simply type-in a search string and VisionGauge� shows you all of the
reports
in which it can be found, twelve at a time. For each matching report,
VisionGauge's�
"Database Search" tools display a thumbnail preview image, along with
two
"key field" strings. Then, when you click on the image of the report
that
you're looking for, VisionGauge� retrieves it from the database and
loads
it into the Report generator.
-
In the Motorized-Stage
Configuration of VisionGauge�, we've added various joystick setting
controls
(to increase or decrease sensitivity to joystick displacement). We've
also
added a command that will allow you to re-calibrate the joystick while
VisionGauge� is running.
-
In the Motorized-Stage
Configuration of VisionGauge�, you can now specify the number of
iterations
to carry out in the "Continuous" run mode.

|